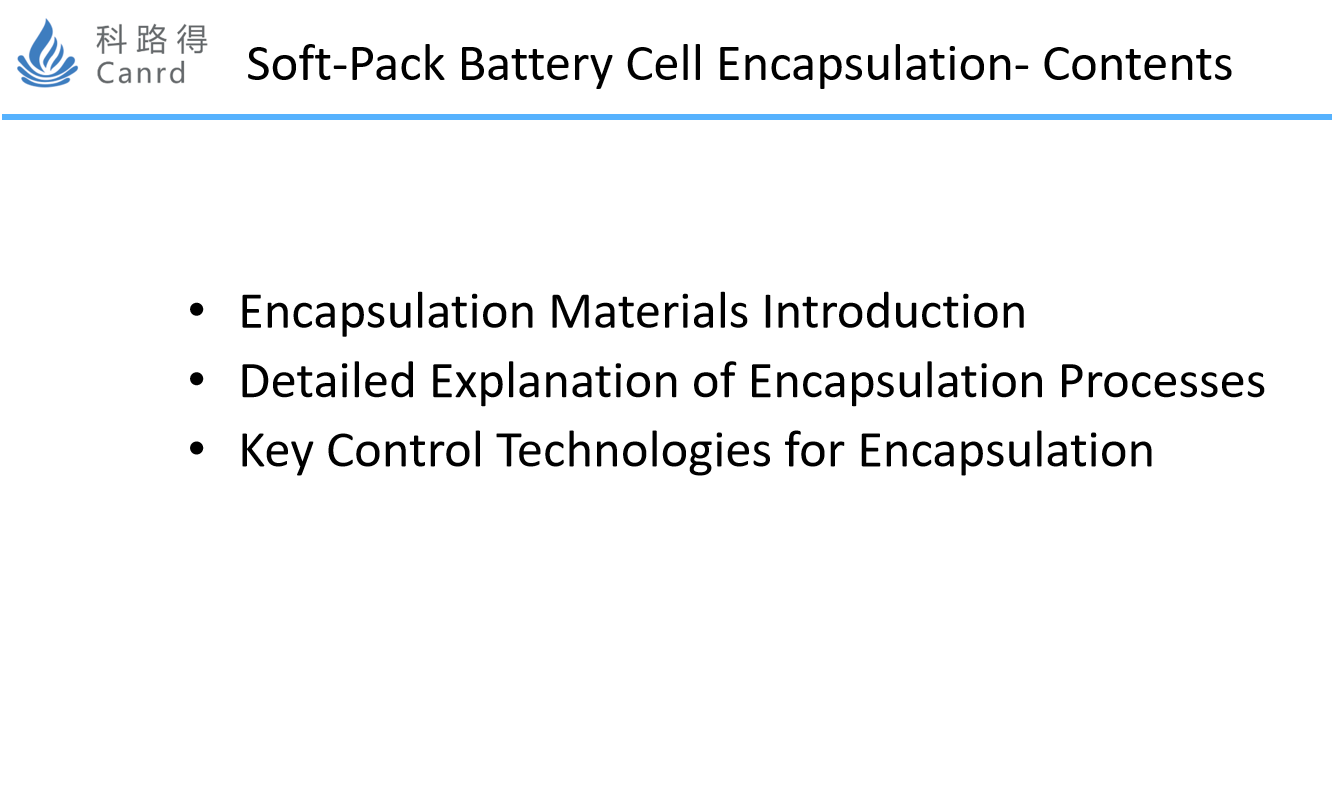
Today's course mainly covers the above three aspects.
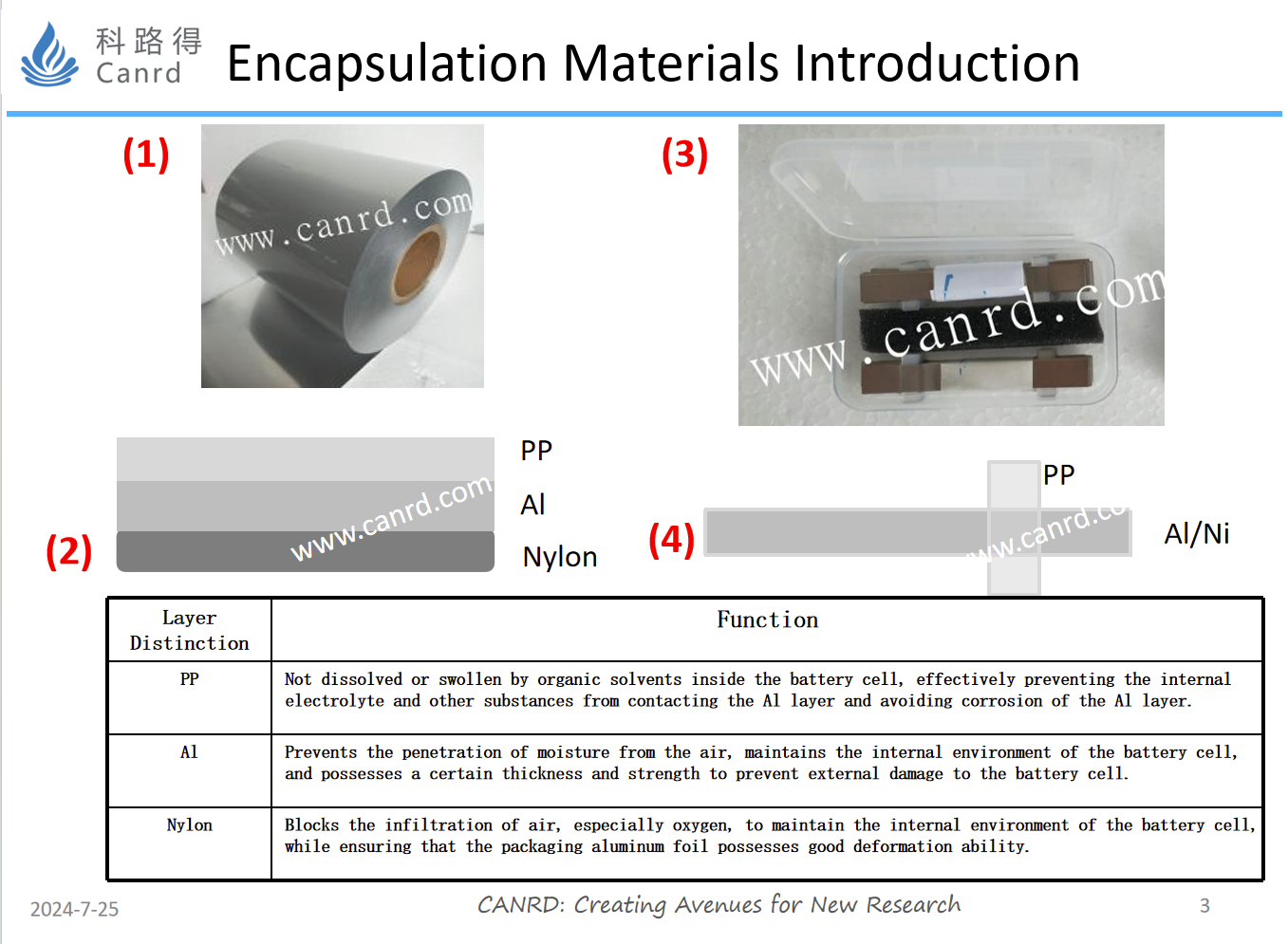
First of all, the two most important materials used in the encapsulation
process: aluminum-plastic film and tabs. Figure (1) above is the physical picture of aluminum-plastic film. At present, there are two appearances of aluminum-plastic film: silver and black. Apple’s batteries are mainly the latter, and others are mainly the former. The aluminum-plastic film is mainly composed of three layers: PP, Al and Nylon layers from the inside to the outside, each layer has its own role, as shown in the table above. The tab is mainly composed of Al band or Ni band plus two layers of PP, as shown in the figures (3) and (4) above. The thickness of the aluminum-plastic film varies from 68~153um.
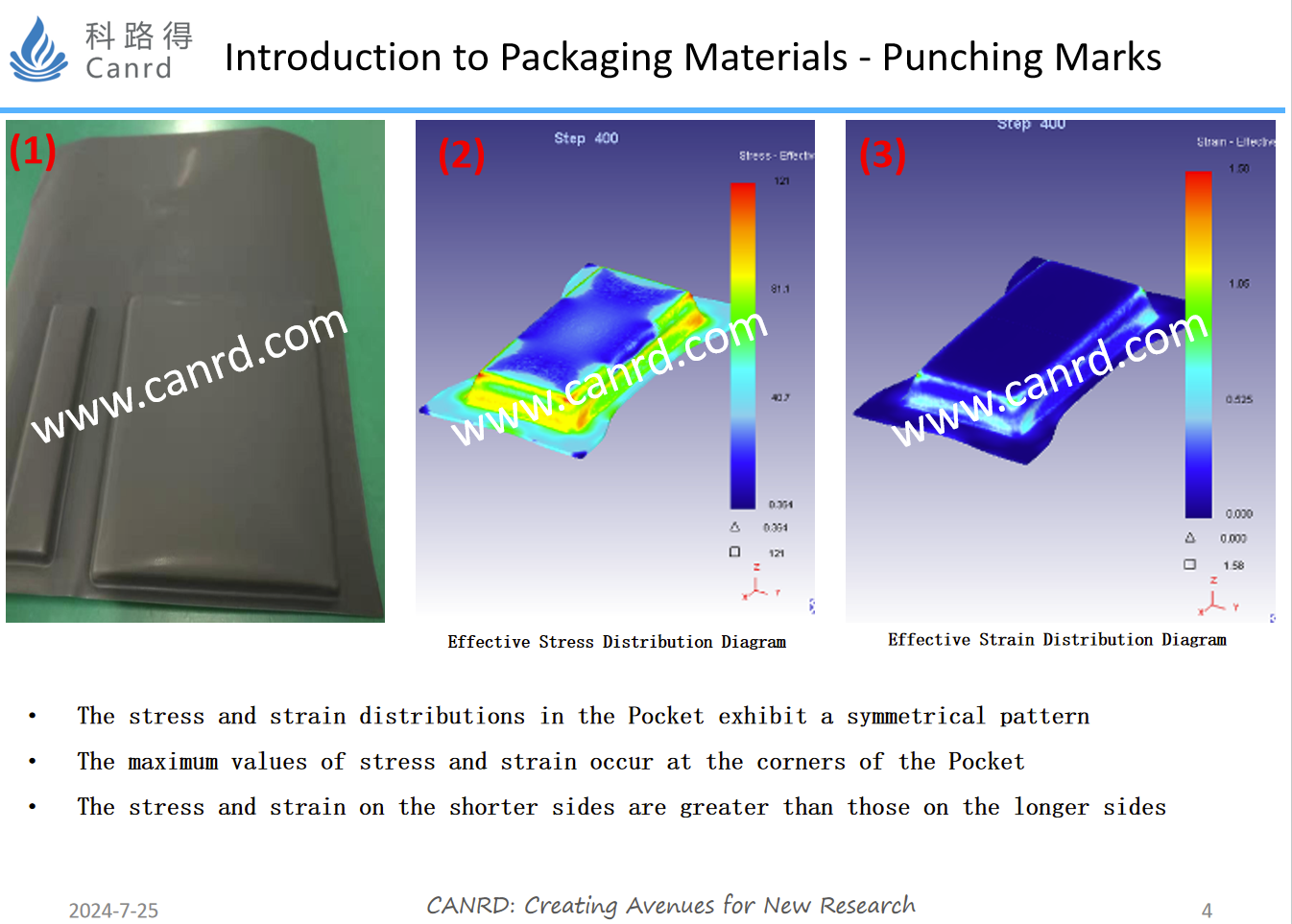
One of the most important properties of aluminum-plastic film is the pit punching performance, and the most intuitive way to display it is the maximum depth of the pit that can be punched. For the aluminum-plastic film punching pit, the pull rise of the top angle position is the largest, and it is the easiest to break, so the maximum punching depth is assessed by assessing the characteristics of the top angle position. Different manufacturers, different thickness of aluminum-plastic film pit depth is different, so we should not buy at will, but consult manufacturers with technical strength, and they will give you some suggestions for use, otherwise it will be troublesome to buy back and have some damage and corrosion. At present, the aluminum-plastic film with good quality is mainly produced by DNP, Showa and Toppen;
In addition, there is a parameter, for the production of the maximum pit depth of the aluminum-plastic film, is not the depth of the top angle breaking, but the thickness of the Al layer in the aluminum-plastic film at the top angle position is not less than 20um (the relaxation standard is 17um) as the basis for judgment.
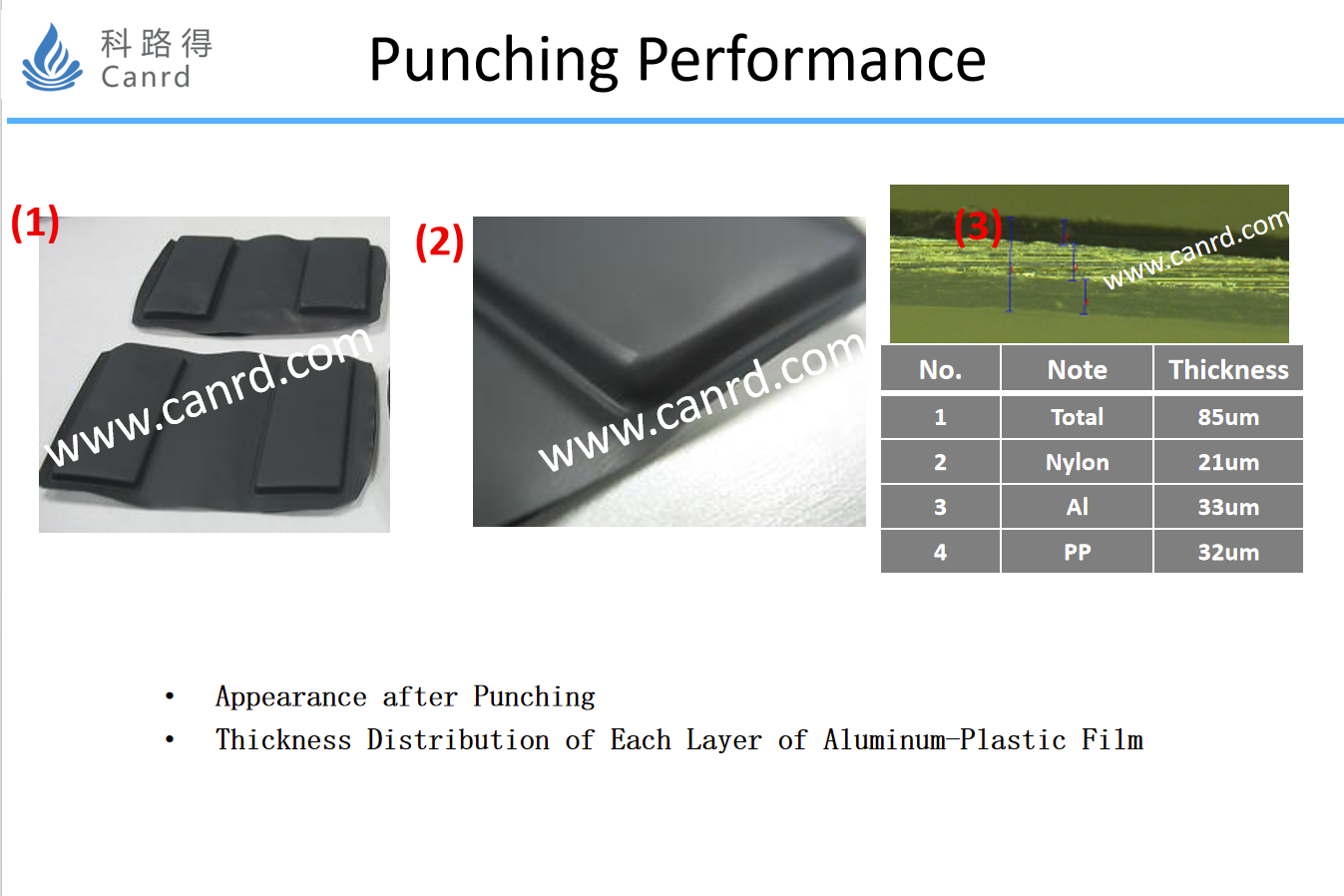
As shown in the figure above, the thickness of each layer is measured when cutting the surface of the aluminum-plastic film. The total thickness is 85um. The thickness of Nylon, Al and PP is 21um, 33um and 32um respectively (the factory specifications are 20, 35 and 30). Due to factors such as test errors and thickness fluctuations, there is a slight deviation between the measured value and the shipping value.
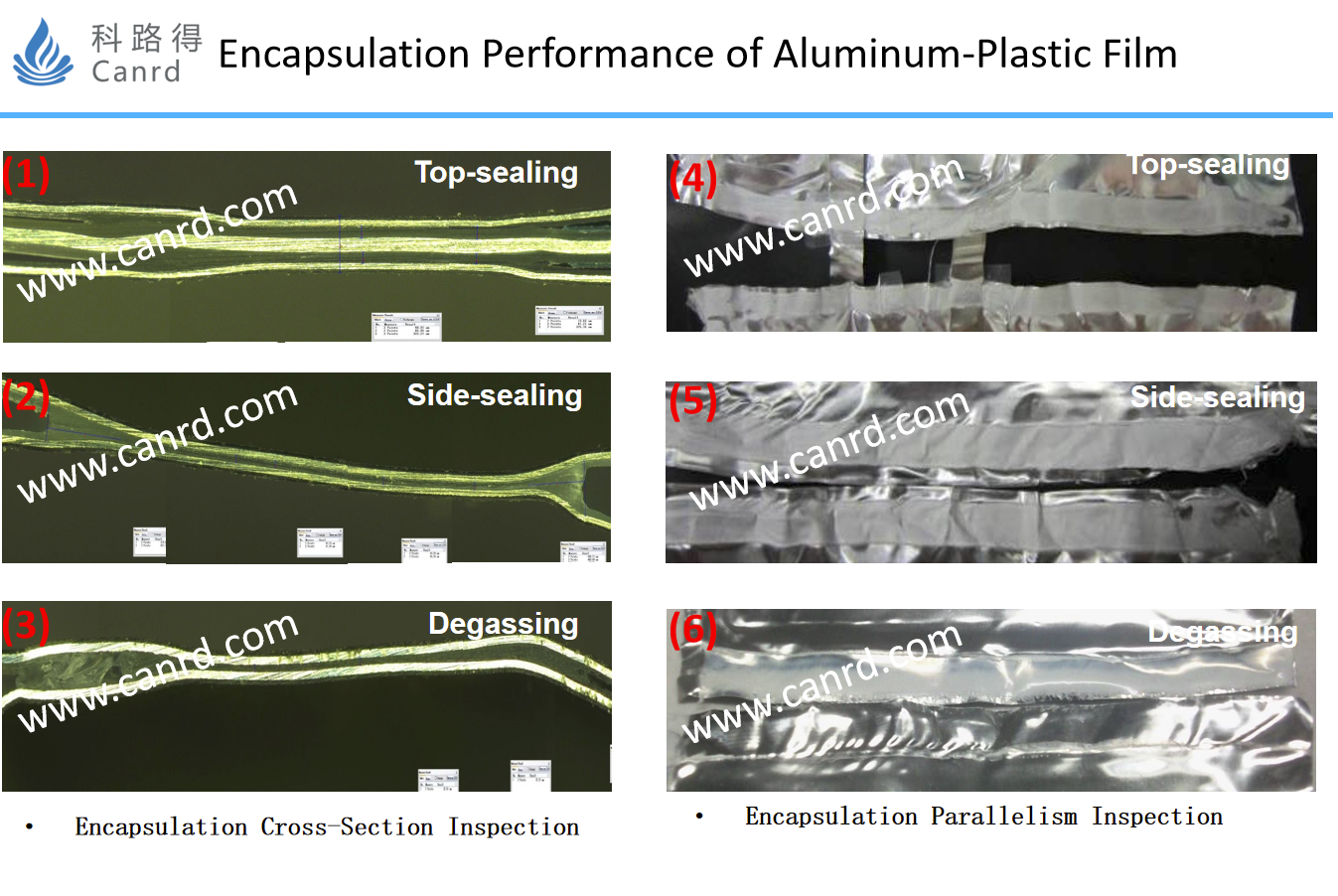
An important basis for evaluating the quality of aluminum-plastic film packaging is to look at the seal section and seal parallelism as shown in the figure above. The cross-section of the seal is to observe the sealing effect in the direction of the vertical seal, mainly to see the appearance of the seal and the thickness of the PP after melting. The above figure (1) is the sealing interface of the top seal, and it is also necessary to observe the parallelism between the tab (white in the middle) and the two layers of aluminum (white strips on both sides) of the aluminum-plastic film, the more parallel the better(The short circuit of the top seal is often caused by the fact that the tab and the aluminum layer are not parallel, or even caused by direct contact). The above figure (4) ~ (6) shows that after encapsulation, tear the seal vigorously to observe the sol effect; Among them, the top side seal is white, and uniform and continuous is the best; When DEG (two seals) are sealed, the material and the shape is different, and the main thing is that it needs to be uniform and continuous.
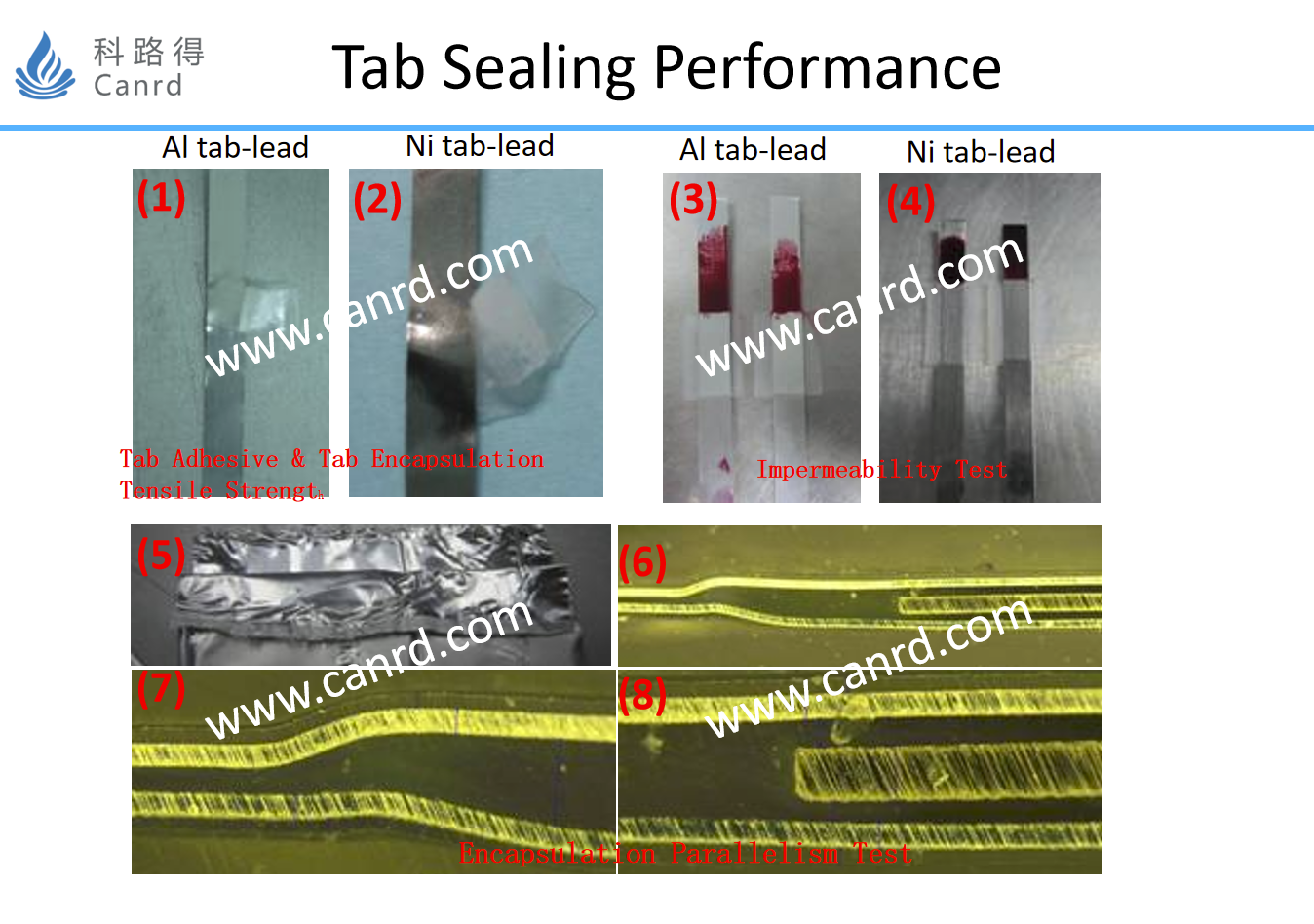
There are mainly aluminum tabs and nickel tabs. The former is used as cathode electrode, and the latter is used as anode electrode. The most important criterion for judging the quality of the tab is the quality of the bond between the tab gel and the tab metal. It is mainly evaluated by stripping and permeate penetration, as shown in Figure (1)-(4). In addition, the tab is the same as the aluminum-plastic film evaluation, and the section surface and the parallelism will be observed after encapsulation. The tabs also have different thicknesses and widths, and according to the needs of the product, the general batteries with large capacity and high rate need to use wide and thick tabs.
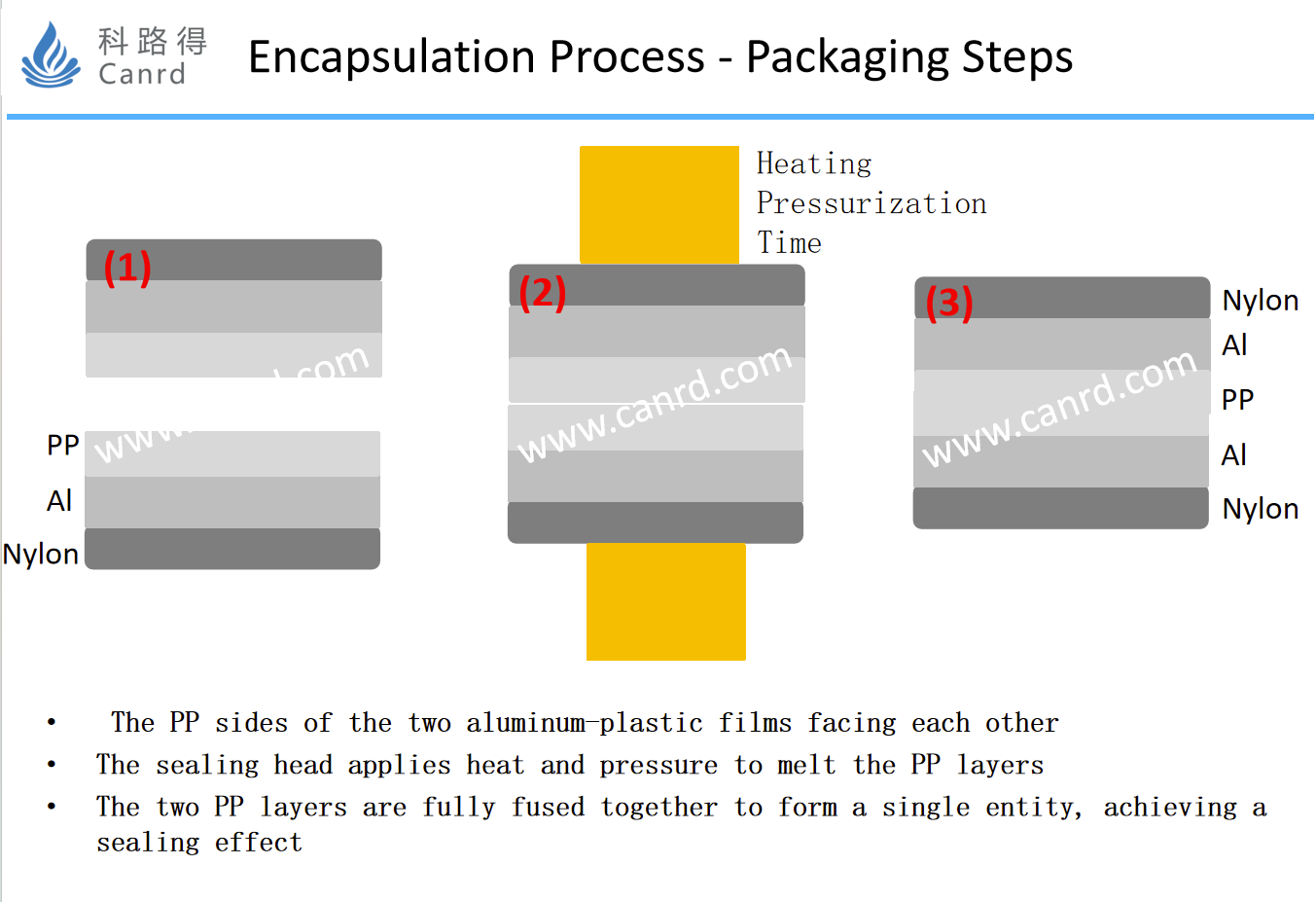
The process of encapsulation is shown in the figure: it is the process of fusing the two layers of PP together by applying pressure and temperature to the head of the aluminum-plastic film. In order to ensure the reliability of the encapsulation, the deformation rate of PP is generally between 25% and 70%.
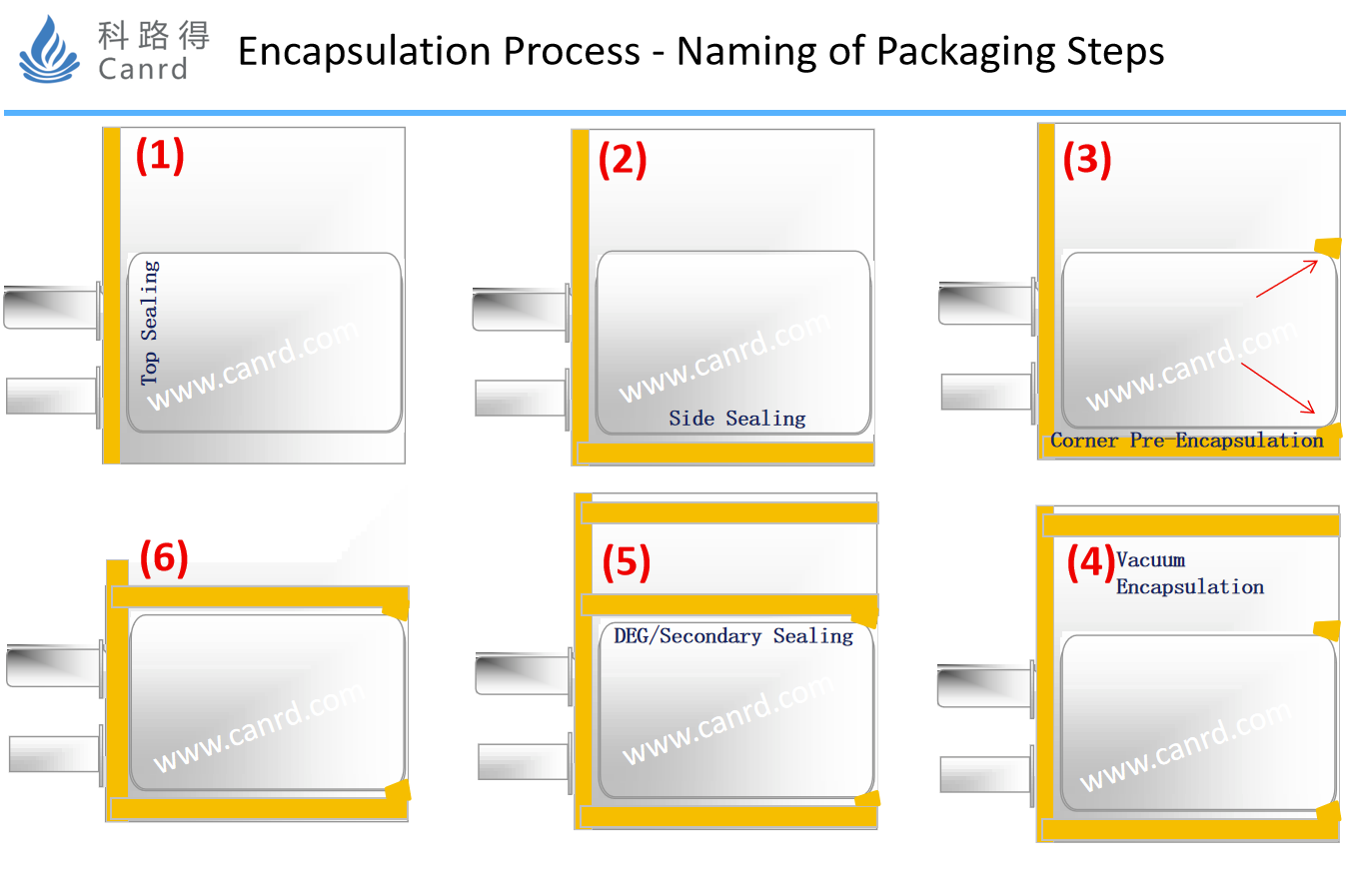
There are five common types of packaging for pouch cells: top seal, side seal, corner pre-pack, vacuum pack, and DEG (two seals). The yellow area indicates the location of the encapsulation, as shown in the figure above, which is the specific location of each encapsulation. Among them, the top seal, side seal, and DEG (two seals) are the most critical; In order to control the encapsulation, the most important thing is to debug the encapsulation machine, which is the most core. If the encapsulation is not done well and the battery leaks, then the battery will basically be scrapped, so the encapsulation is very critical.
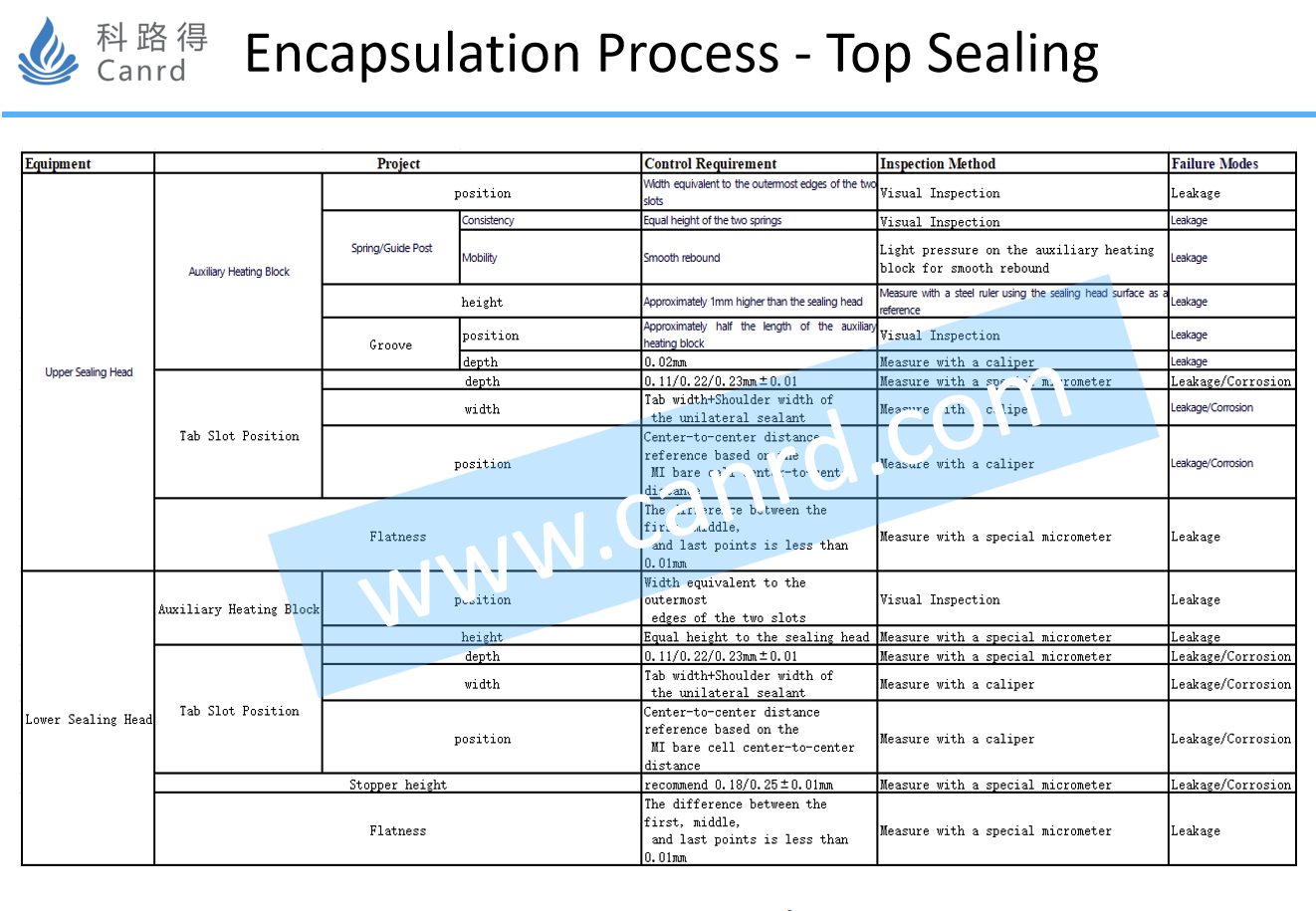
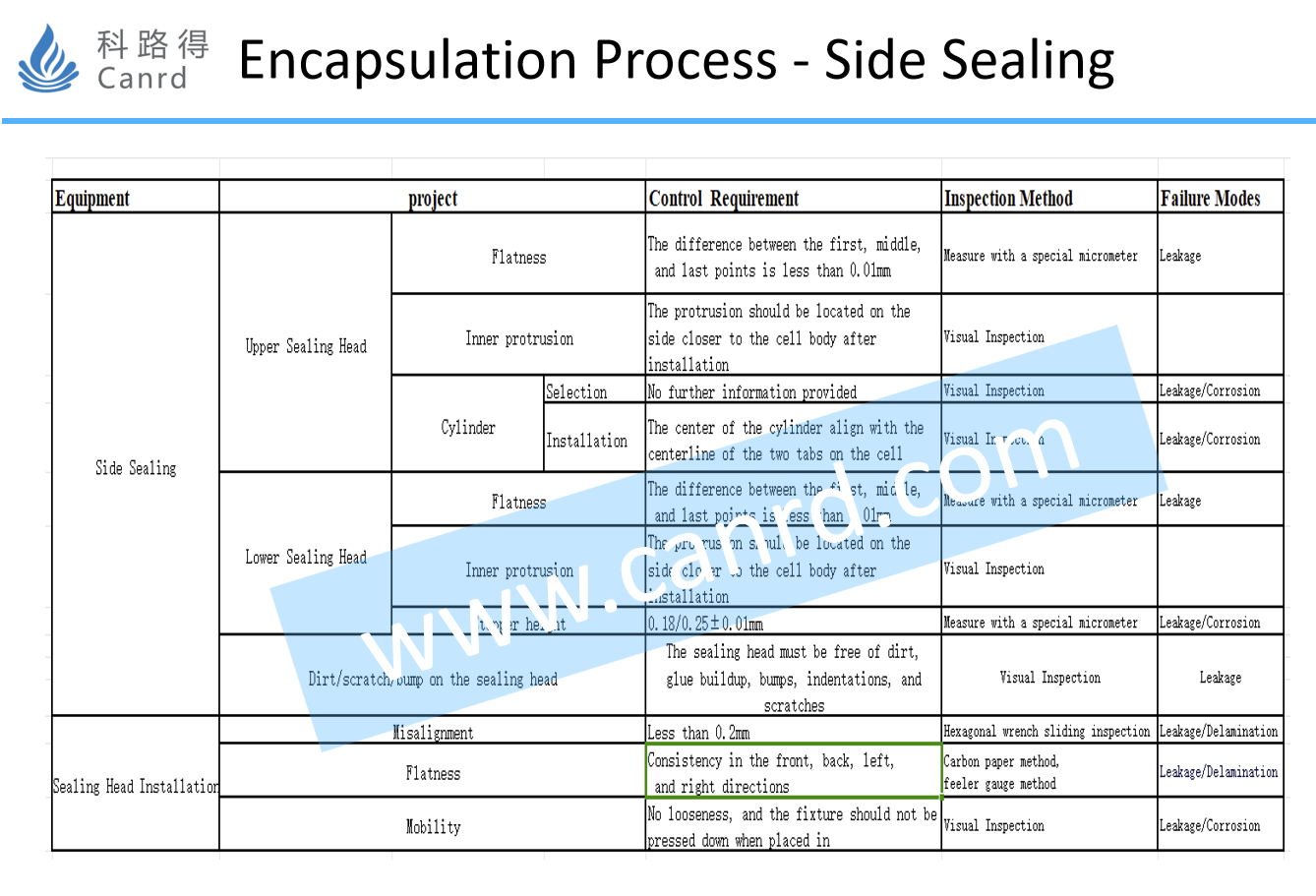
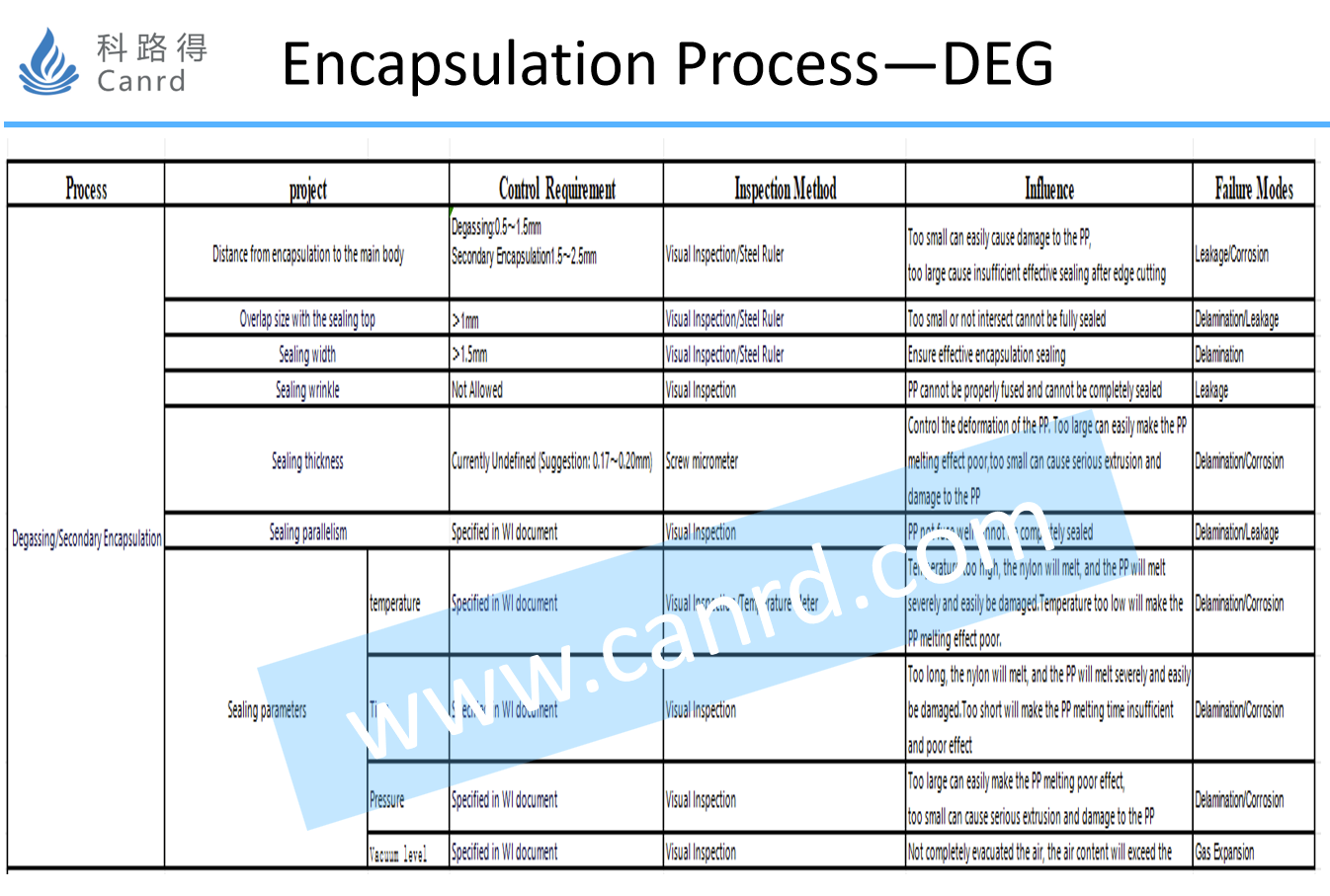
The above is the specific description of the encapsulation and adjustment machine, which is all practical experience, and must also be combined with the corresponding encapsulation machine.
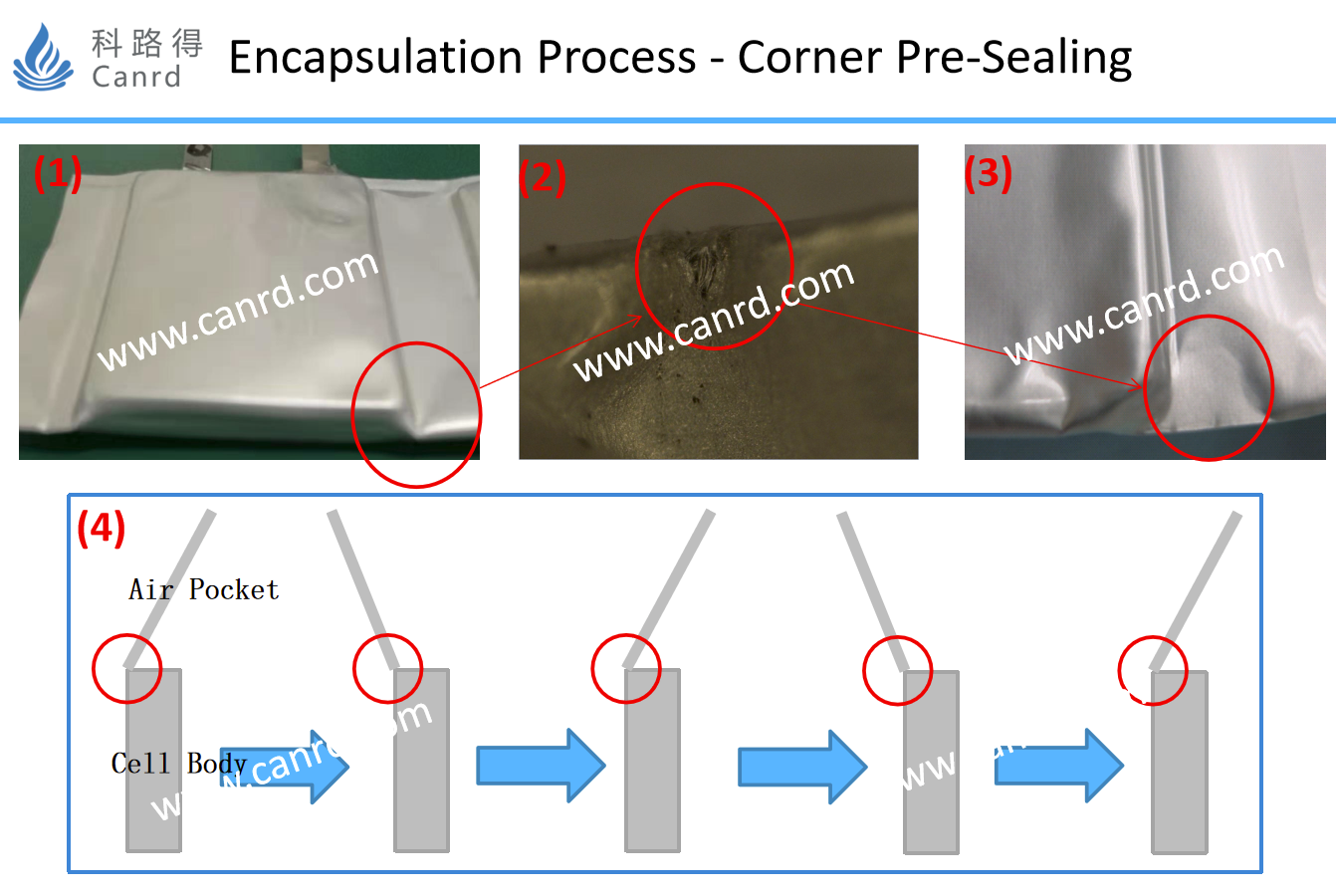
Corner pre-encapsulation, as shown in the above figure (1) and (3), is to simply encapsulate the two bottom corners of the battery cell to make the two layers of aluminum-plastic film stick together. The main purpose is to increase the bending resistance at the bottom corner. The main reason in the above figure (2) is the damage of the bottom corner caused by bending, as shown in the above figure (4), in the battery production process, the battery cell air bag will often be touched, so that the position of the air bag and the battery cell body will be bent back and forth, resulting in damage.
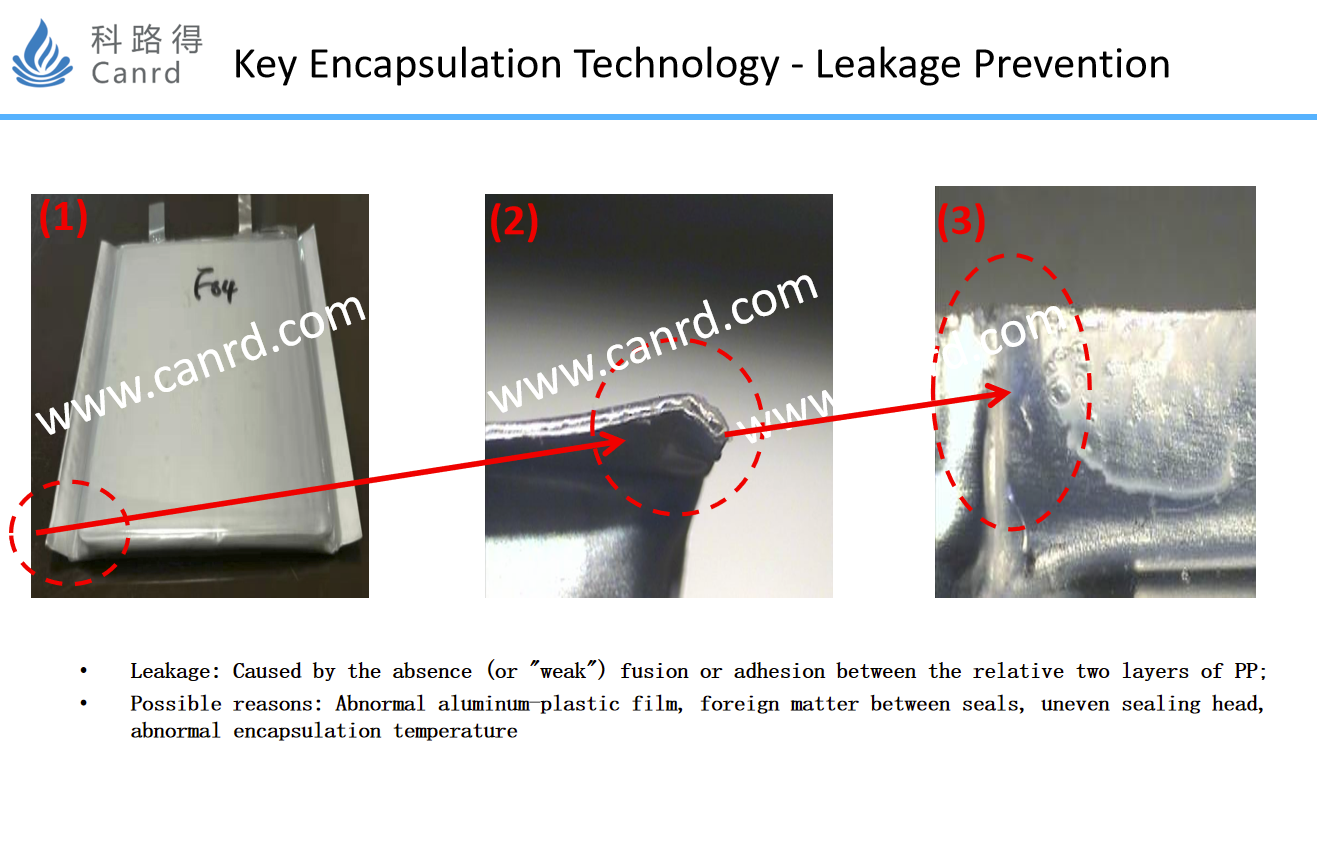
Encapsulation leakage, this is easier to understand. It is that the seals are not completely fused together when encapsulation, resulting in poor sealing effect and leakage. As shown in the figure above, it is a cause of failure of encapsulation leakage. This is also easier to check: it is generally to tear the seal open and observe it directly.
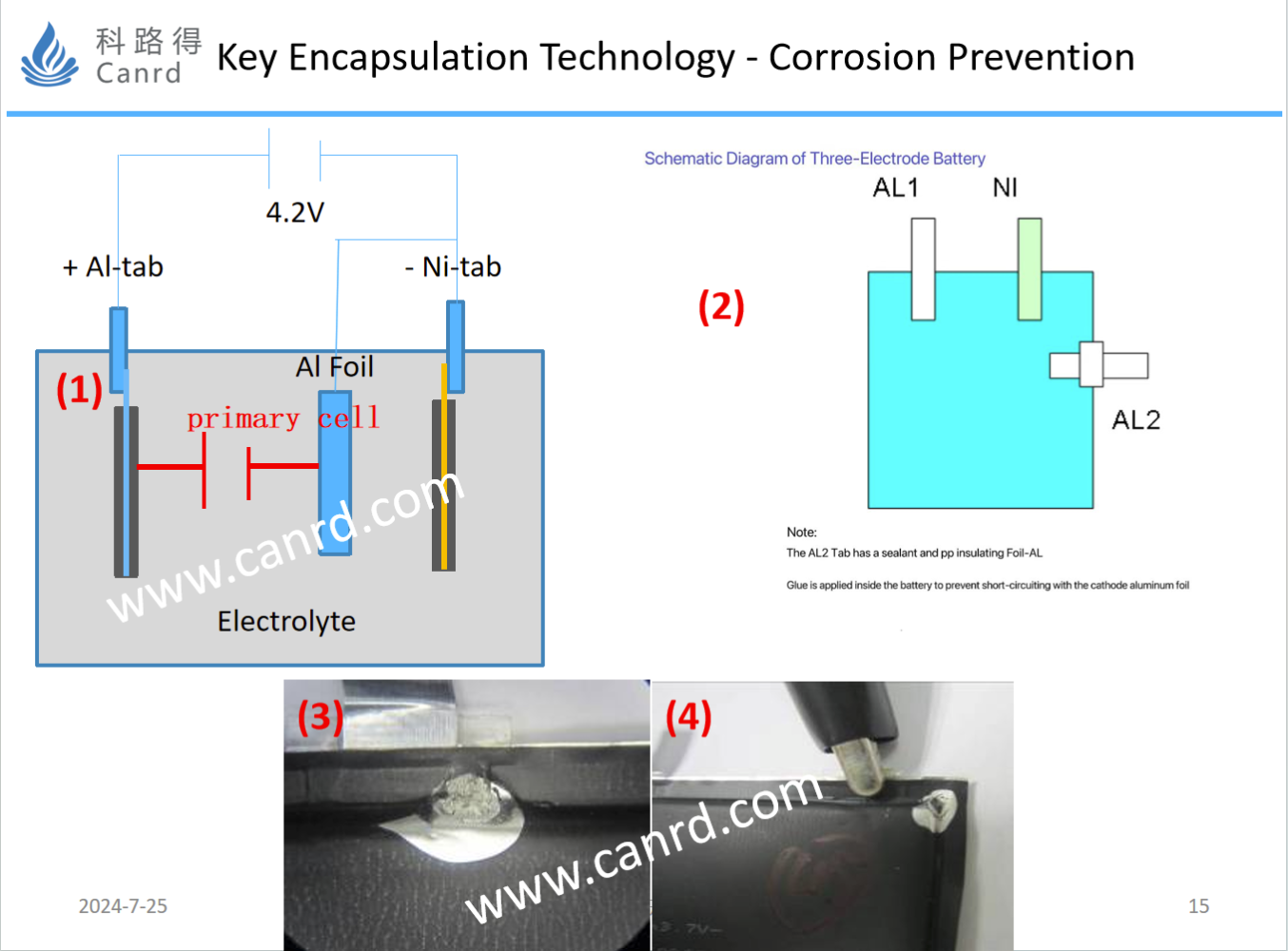
Encapsulation corrosion is also a common problem. For this encapsulation problem to occur, two conditions must be met:
1. There is a short circuit or a micro-short circuit between the Ni tab and the Al of the aluminum-plastic film;
2. The Al layer of the aluminum-plastic film is in contact with the electrolyte (that is, the PP layer is damaged).
At this point, the Al layer of the aluminum-plastic film will form a primary battery structure with the cathode electrode, spontaneously discharging, and then the Al layer of the aluminum-plastic film will act as the anode electrode, undergoing a dissolution reaction.
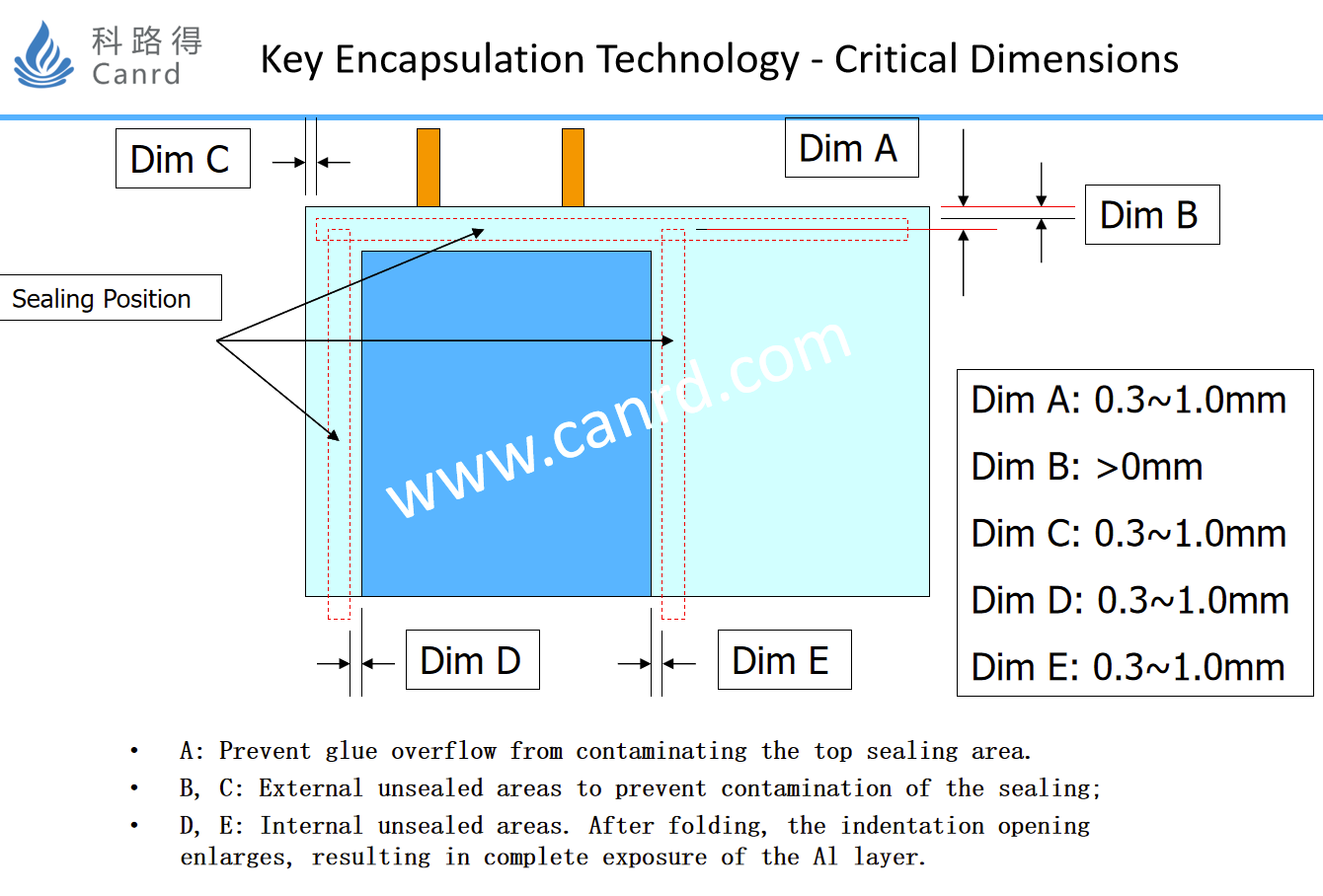
Finally, for encapsulation, there is also a very important assessment indicator: key dimensions. To achieve excellent encapsulation results, it is necessary to strictly control the size of the seal. The above figure briefly summarizes the encapsulation size indicators of the following core components, which can be referred to by everyone.